Projects
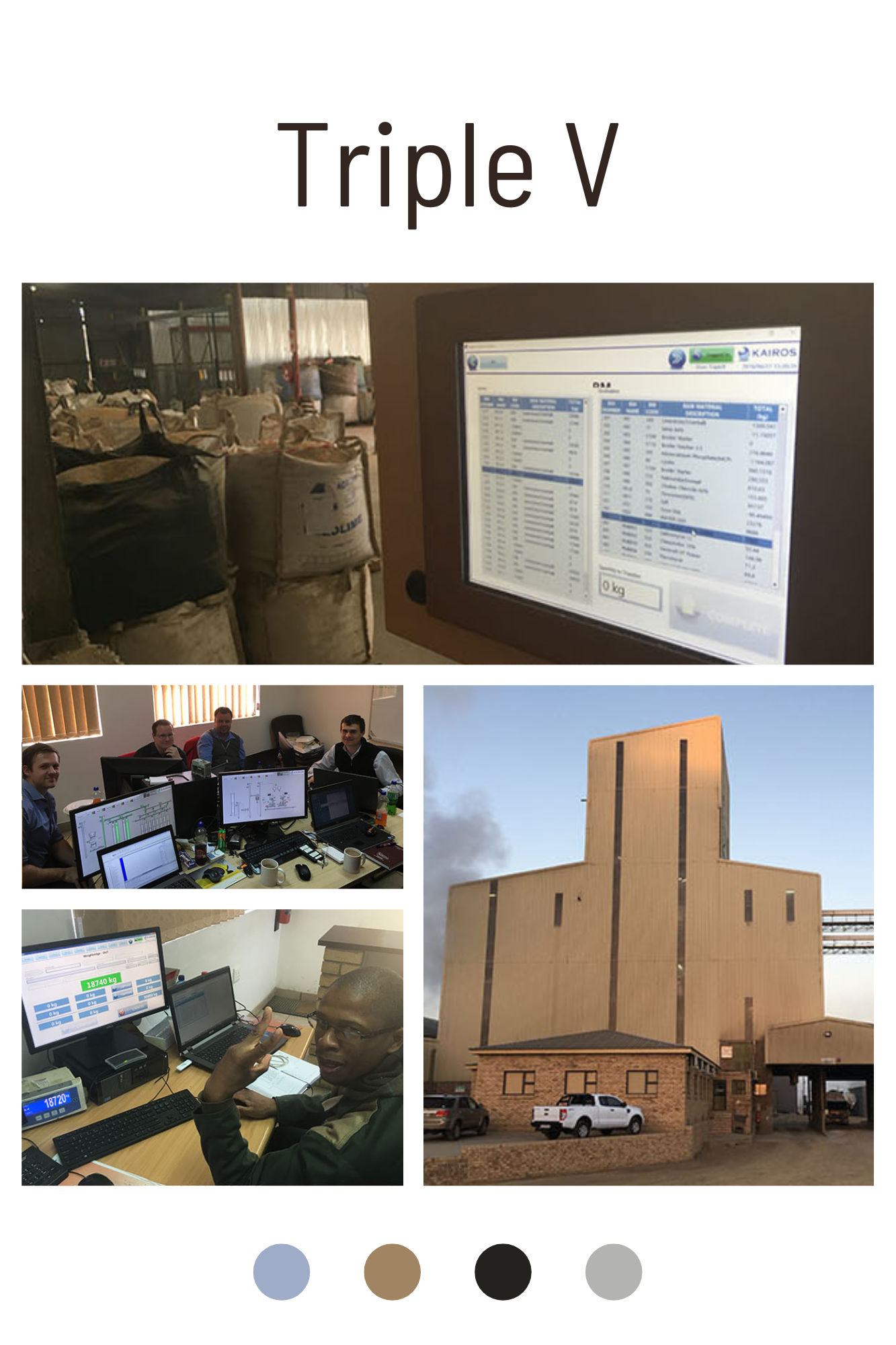
Triple V Animal Feed
Project Scope:
Complete upgrade of Plant Automation and Management systems including:
- Security
- Weighbridge
- Intakes, Bunkers & Raw Material management
- Batching Control
- Recipe Management
- Production Scheduler & Forecast
- Traceability
- Outloading with ability to load per compartment
- Stock Management
- Extensive Reporting & integration
- Quality module
Project Completed Date:
November 2016
Client Testimony:
“Customized to our specific needs”
“Availability of plant data”
“Kairos very committed to the project”
“Excellent after sales support – they do not leave you alone”
“ Ability of their system to integrate to other systems”
“Local South African based company”
“Very fast and excellent level of Reporting“
“Assistance with process improvements”
“Experienced in system design and instrumentation”
“The Automill system showed us many gaps in our processes”
“Improved Stock Control”
“Eagerness to satisfy our specific needs”
Kobus du Toit – General Manager TripleV Feeds
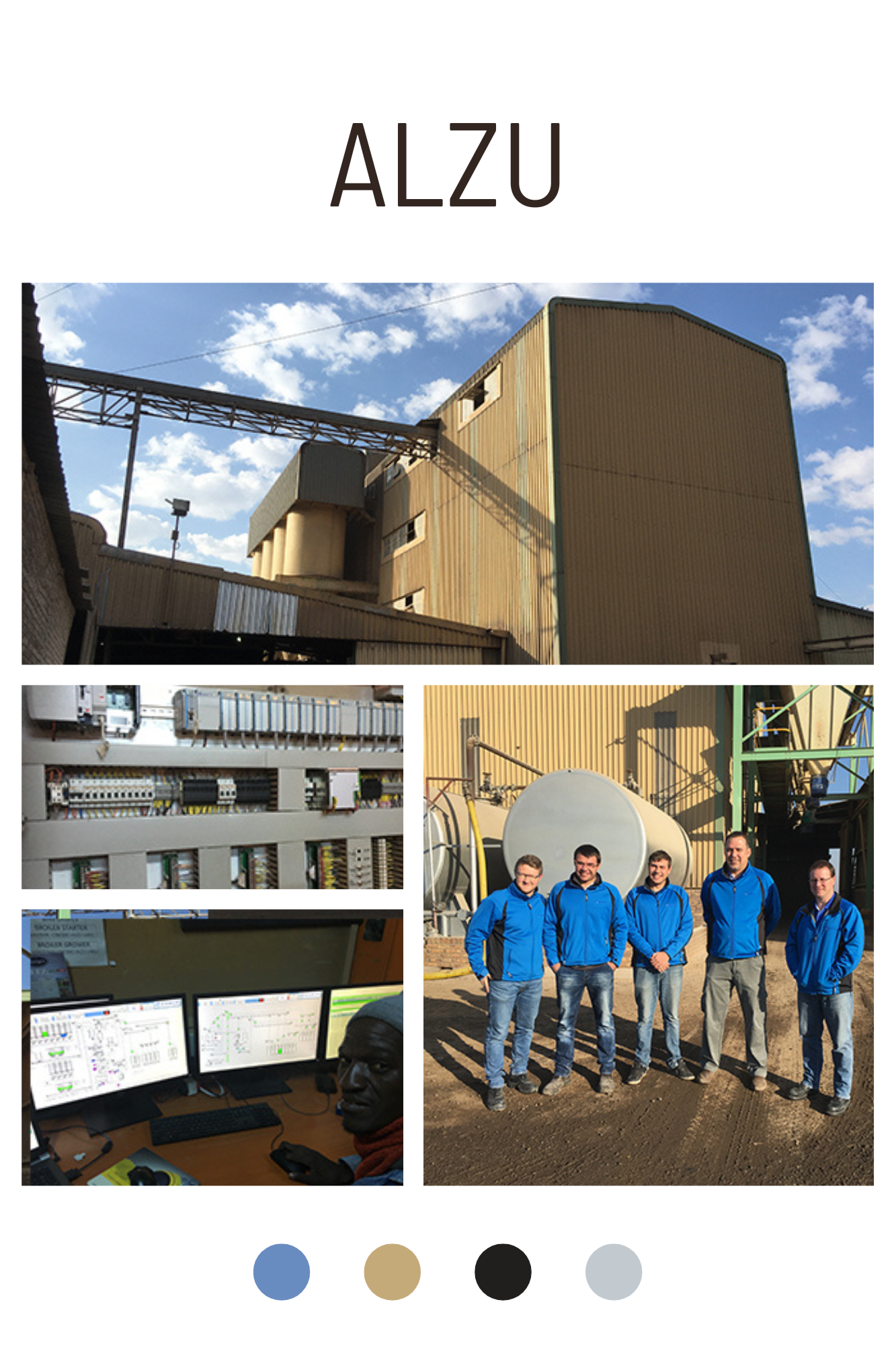
ALZU Feeds
Automill Solution
Project Scope:
Upgrade of Plant Automation and
Management systems including:
- Intakes
- Batching Control
- Recipe Management
- Production Scheduler & Forecast
- Hand Additions
- Reporting & Integration
Project Completed Date:
June 2017
Client Testimony:
“A well planned and professionally rolled out project”
“Kairos staff are skilled and well equipped to complete tasks at hand”
Kelly Cornelius – ALZU
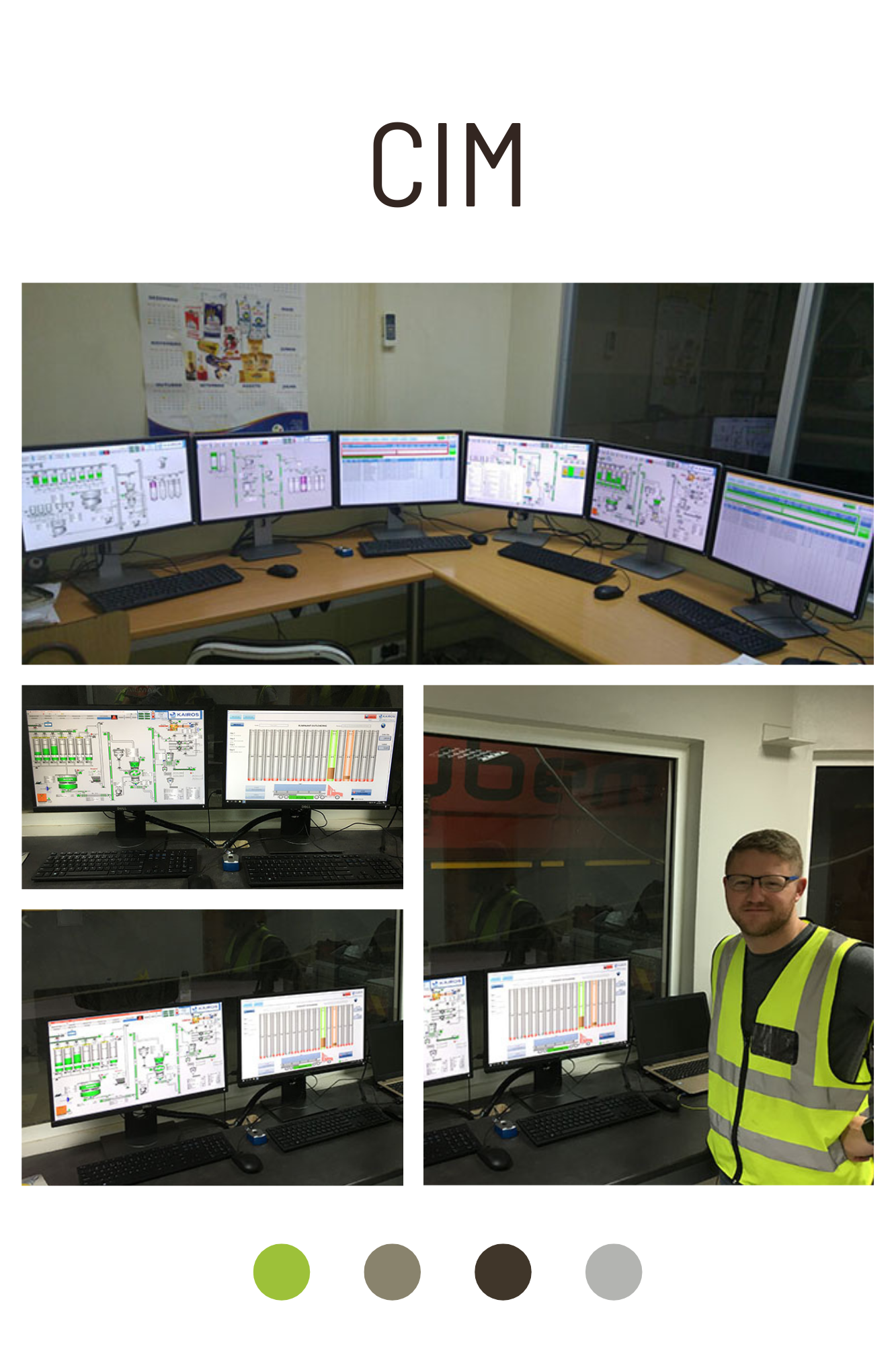
CIM Feeds
Project Scope:
New Ruminant plant Automation and
Management systems including:
- Intakes
- Batching Control
- Bunkers & Raw Material management
- Recipe Management
- Production Scheduler & Forecast
- Hand Additions
- Traceability
- Outloading system
- Packing system
- Reporting & Integration
Project Completed Date:
October 2016
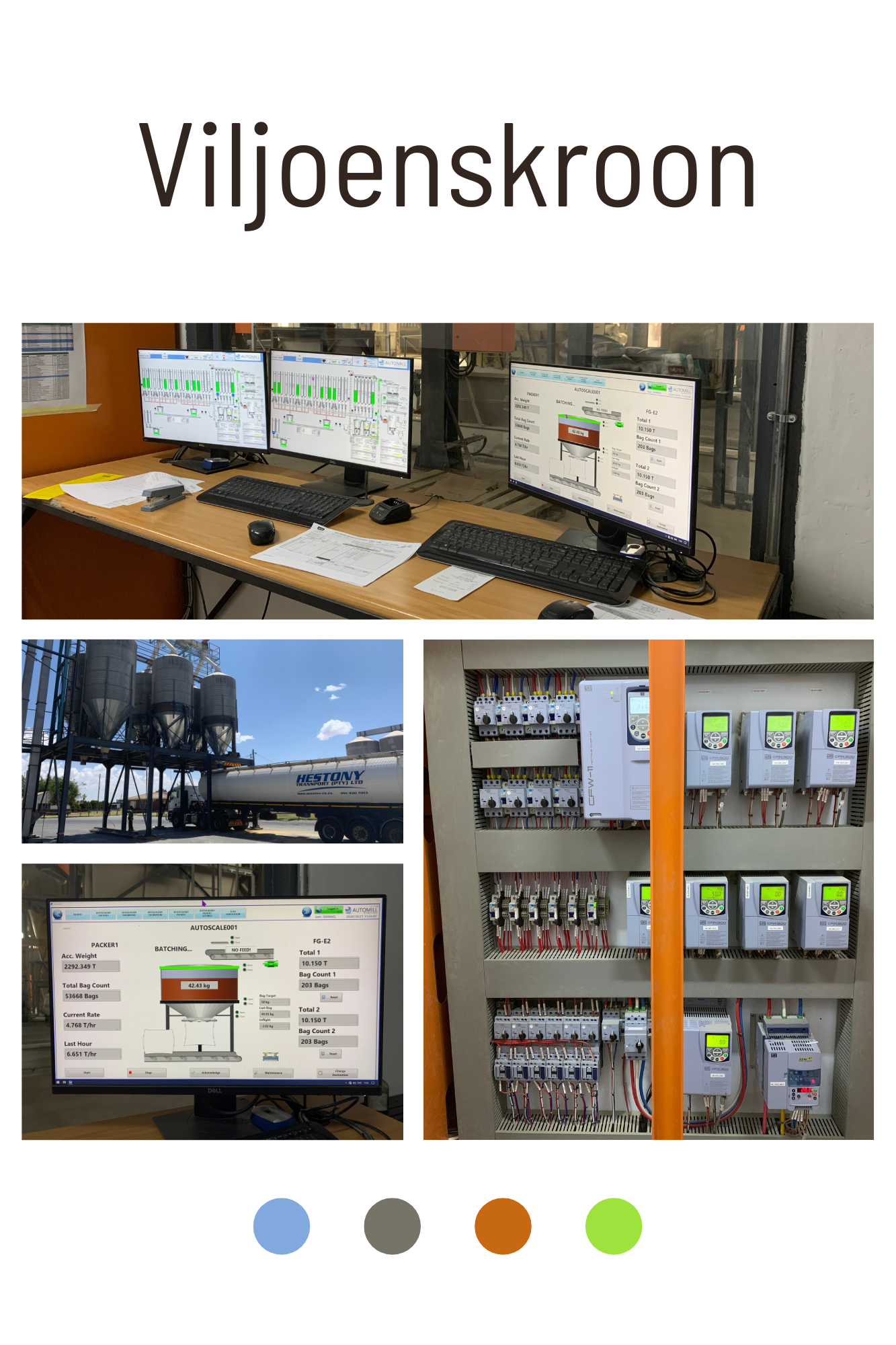
Nutri Feeds Viljoenskroon
Project Scope:
More control to ensure constant production throughput and quality of their feed:
- Improve product quality, as it is inconsistent.
- Get batching accuracy up to their group standards.
- Reducing human labour, and human error and the system should guard against contamination between recipes.
- Be more cost-effective to stay a leader in the market, as their current process is inefficient.
- Renew all MCC & electrical hardware and field instrumentation.
Automill Solution & Results:
- Weighbridge intakes to production, pelleting and finally Outloading, all processes were Automated and are now operated by one person in a central control room.
- Removing the human control aspect, they have achieved incredible accuracy that results in much better stock management, as well as a consistent quality on their final product.
- Nutri Feeds has subsequently added a 3rd pelleting line to meet their new demand, as the plant is operating much more efficiently than before, and their mixing capacity has increased consistently to accommodate additional pelleting capacity.
Client Testimony
“I do believe we have much better quality now due to the accuracy we
get, as well as much higher throughputs than before. That means lower
costs per tons to produce and makes us more competitive in the market. From a reporting side we can see everything that goes on in our plant and fix problems much faster thanks to better visibility.” Johan van Zyl – National Operations Manager

Nutri Feeds Bloemfontein
Project Scope:
More control to ensure quality of their feed:
- Improve product quality, as it is inconsistent.
- Get accuracy up to their group standards.
- Reducing human labour, and human error.
- Be more cost-effective to stay a leader in the market.
- The plant runs on average 6000 tons/month, and they want to increase to 8000T/month.
Automill Solution & Results:
- From intakes to production, pelleting and finally outloading, all processes were Automated and are now operated by one person in a central control room.
- By removing the human control aspect, they have achieved incredible accuracy that results in much better stock management, as well as consistent quality on their final product.
- In the first 6 months, they exceeded their initial goal and reached a new record of 9000 Tons/month. By constantly using the Downtime information that indicates where valuable time is being wasted, they further increased their throughput
to 10,000 within the following 6 months. All of this was achieved while still maintaining the quality they expect.
Client Testimony
“I do believe we have much better quality now due to the accuracy we
get, as well as much higher throughputs than before. That means lower
costs per ton to produce and makes us more competitive in the market. From a reporting side, we can see everything that goes on in our plant and fix problems much faster thanks to better visibility.” Johan van Zyl – National Operations Manager